One of the services offered by our company is professional gas cutting. Currently, this is one of the most common and efficient methods of separating low-alloy and low-carbon steel.
Gas cutting offers tremendous opportunities – this method allows you to process material from 3 to even 300 mm thick. Due to its characteristics and the high temperature generated during cutting, it is not recommended for use with thin sheets.
Gas cutting is one of the more popular methods of separating various metals. It involves bringing the selected material to its ignition temperature. The next step is burning and blowing off the liquid metal oxides thanks to a high-pressure oxygen jet. Gas cutting is effective due to the appropriate design of the torch, which blows out oxygen mixed with combustible gas. Usually acetylene or propane-butane are used in this method. These gases make it possible to obtain high temperatures in a short time.
Interested
in our offer?
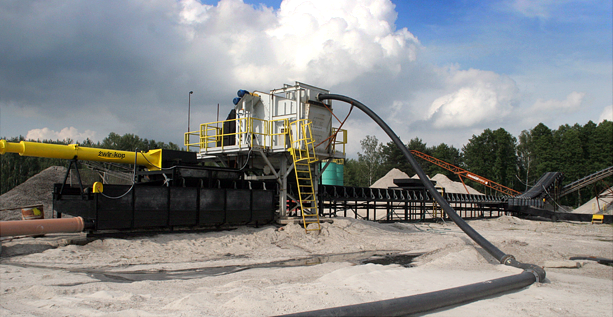
What does gas cutting consist of?
Gas cutting, also known as oxyfuel cutting or gas burning, is a complicated process and can only be performed under certain conditions. The material to be separated is heated to a maximum temperature – the so-called ignition temperature. At the designated point, the liquid metal is blasted with a stream of oxygen. The amount of pressure is adjusted to the selected gas with the help of which oxygen burning is performed and to the thickness of the material.
Modern gas cutting usually uses acetylene or propane to achieve the desired burning temperature. The acetylene-oxygen firing method makes it possible to reach a high temperature very quickly, while the propane-oxygen method is more economical and therefore more widely used in automated plants.
Oxygen firing
It allows the cutting of flexible sheets by heating the sheet properly and burning it in the desired location. The sheet is ignited and oxidized. The powdery metal oxides formed in the process are removed with a strong jet of gas. Oxygen firing requires a suitable mixture of oxygen and the selected gas, which is applied to the sheet at right angles. This results in high precision cutting. It is worth remembering that the lower edge of the cut surface may produce the so-called slag. In turn, the upper edge is usually rounded. With this method, it is possible to cut metal sheets of considerable thickness, up to 300 millimeters. In it, the edges of the processed metal sheets are set at right angles to each other, which facilitates their subsequent use.
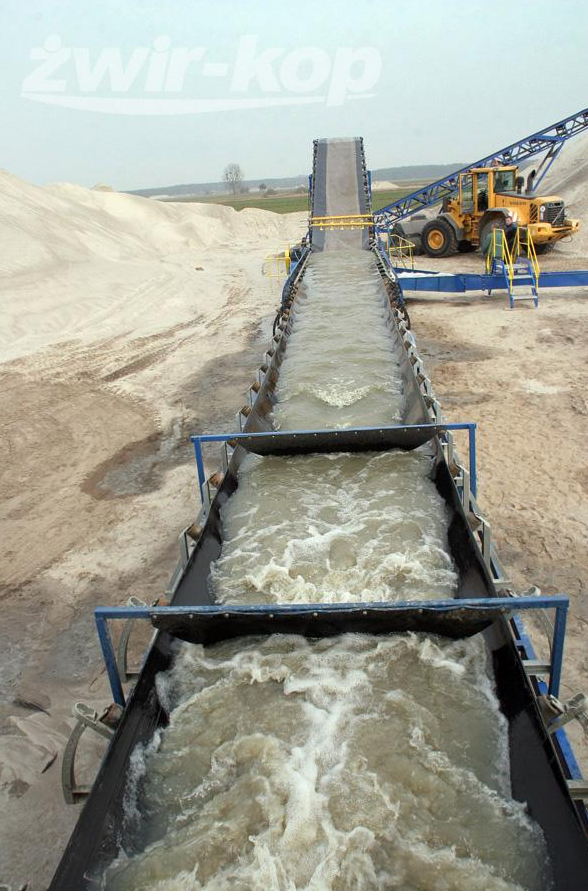
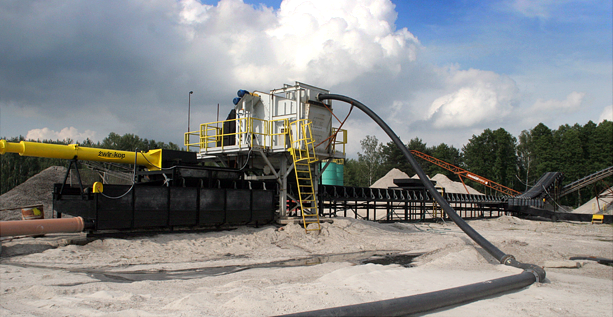
Advantages of burning with oxygen
The oxygen firing method we offer allows us to perform cutting of steel of different thicknesses, thus increasing the range of applications. Due to its relatively low operating costs, it provides the possibility of fully automating the gas burning process. As a result, you get surfaces separated precisely, evenly, with perpendicular, aesthetic edges. It is possible to process the material at any angle.
Gas firing
It is a very economical method of obtaining metal elements in the desired sizes and shapes. It is particularly effective in the processing of low-carbon and low-alloy structural steels, as well as sheets covered with rust. Gas burning, thanks to the use of appropriate proportions of oxygen and gas, allows for the achievement of optimal efficiency of the sheet metal cutting process.
It usually uses gases such as:
The flame used allows for the removal of rust, paint and any impurities from the processed material. As a result, excellent quality of cut edges is achieved.
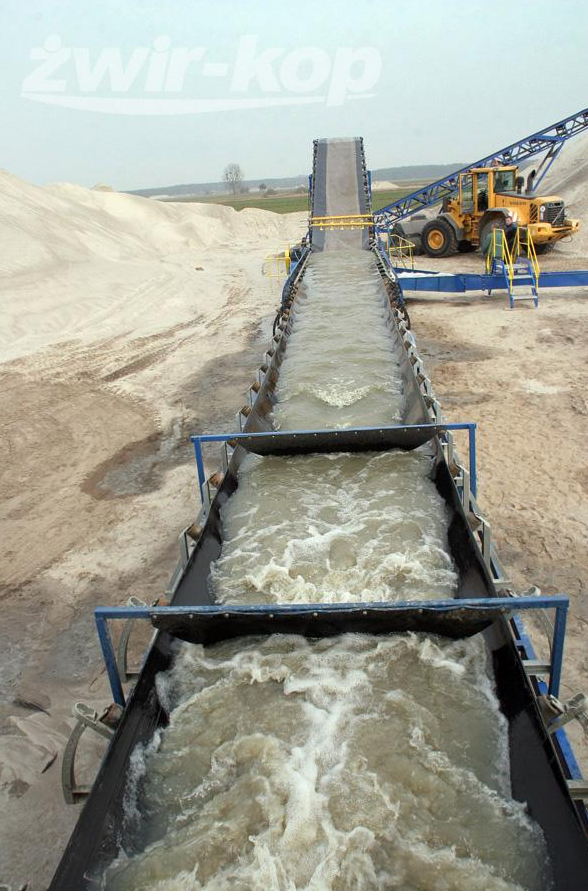
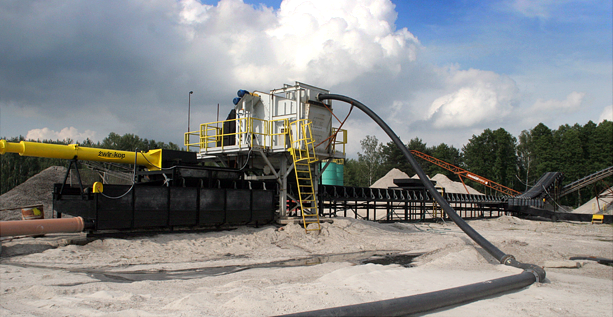
Wide range of applications of gas cutting
The oxygen burning method is used both in amateur workshops and in large production plants. This technology is used in the precise processing of popular metals such as brass, cast iron, bronze or steel itself – not only for their precise cutting, but also for soldering, heating and firing. Due to the above, this method is considered fully universal.
Why is it worth choosing gas cutting from us?
In the field of modern, thermal processing of steel, we have vast knowledge and necessary experience. A qualified team of specialists working on modern, automated devices is responsible for the execution of orders. Thanks to this, the effect of the work performed is always more than just satisfactory.
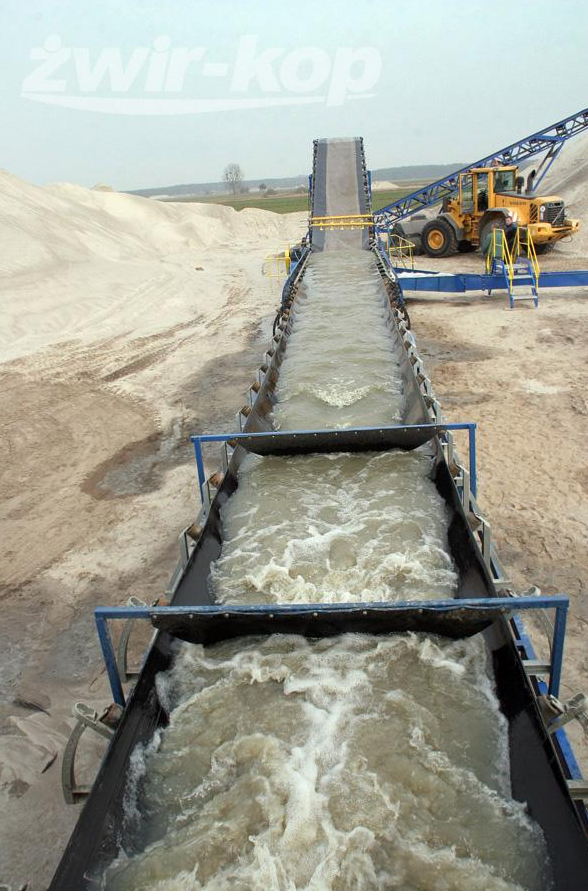